The Porsche Taycan was the first production vehicle to make use of an 800V electrical system. Here’s how it works
Words: Shane O’Donoghue
Porsche didn’t cut corners in the design and development of the Taycan, its first modern fully electric vehicle that shares its platform with the similarly impressive Audi e-tron GT. Regardless of which Taycan you go for, they all share the same fantastic innovation: the world’s first 800V electric vehicle architecture. For context, the highest voltage usually employed is 400V, so that’s quite a jump. But what exactly does this mean?
Porsche offered us a first glimpse of its electric intentions when it unveiled the Mission E concept car at the 2015 Frankfurt Motor Show, and crowds were duly wowed. The production Taycan closely follows the Mission E’s design, but perhaps of more importance was Porsche’s announcement that the production car would carry the first ever 800V drive system. The brand’s press team alluded to a few of the advantages of such a setup, including lower kerbweight and faster charging times than offerings from other manufacturers – but to understand Porsche’s desire to double the voltage in the Taycan’s electrical system, you have to do some maths.
With any given electric car, the battery pack has an energy capacity, usually referred to in terms of kWh (kilowatt hours). Think of this as analogous to the amount of petrol that can fit into a fuel tank. The larger the energy capacity of the battery pack, naturally, the longer it will take to ‘fill up’, but just as every petrol car uses its fuel in varying levels of efficiency, electric cars use the energy in their batteries at different rates. That’s not so important here, because EV technology focuses on recharging the battery. In other words, it’s chiefly concerned with getting energy back into the battery, rather than how the energy is taken out.

Porsche EV charging system
A simple equation explains the relationship between the required energy (E), the time (t) and the electrical power applied (P): E = P x t. This calculation means a 100kWh battery would, theoretically, take an hour to charge from flat to full at a power rate of 100kW, if it were possible to do such a thing in such linear fashion. That’s by the by. The important thing to take from this is that, to reduce the time taken (t) to transfer a given amount of energy (E), the power needs to be increased. We need to dig into that power rate (P) a little more. In this case, the power is calculated by multiplying the voltage (V) and current (I): P = V x I.
With this in mind, if you can increase either the voltage or the current (or both), without reducing the other, then the power also increases and charging time reduces. It sounds simple. Unfortunately, there are limitations when it comes to electrical current, the problem boiling down to the thickness of cables and even the pins in the charging plug.
A current through a wire is defined by the flow of electrons that passes through it. As it does so, the electrons bump into the atoms of the material the wire is made from, transferring some of their kinetic energy to the wire, which results in an increase in temperature. In turn, this temperature increase heightens the resistance of the wire. Resistance (quoted in ohms after a German physicist, Georg Ohm) measures the ‘opposition’ to current flow. Indeed, Ohm’s Law states that, for a fixed voltage and temperature, more resistance means less current.
This is a way of saying that the current you can put through a wire/cable is limited – a thinner cable will increase in temperature (and hence resistance) sooner than a thicker one. Big, heavy charging cables could be used to allow for higher currents, but the pins in the charging plugs would end up being the bottleneck at some stage. Cooling of the wiring and connections is a feature of many chargers, but Porsche felt it needed a different approach to achieve its aim, which is why instead of looking to increase current, engineers went back to the P = V x I equation and focused on voltage.
In the early stages of the Taycan’s development, most other electric cars (and electric car chargers) maxed out at around 400V. Porsche was determined it would advance the game for high-performance electric cars, meaning fast charging was a priority, but it couldn’t come at the expense of long range between charges. The scenario we were provided with gave an example of a typical long-distance drive across Germany, illustrating how the average speed someone could achieve over that journey in an electric vehicle strongly correlated with the speed at which the car could be charged.
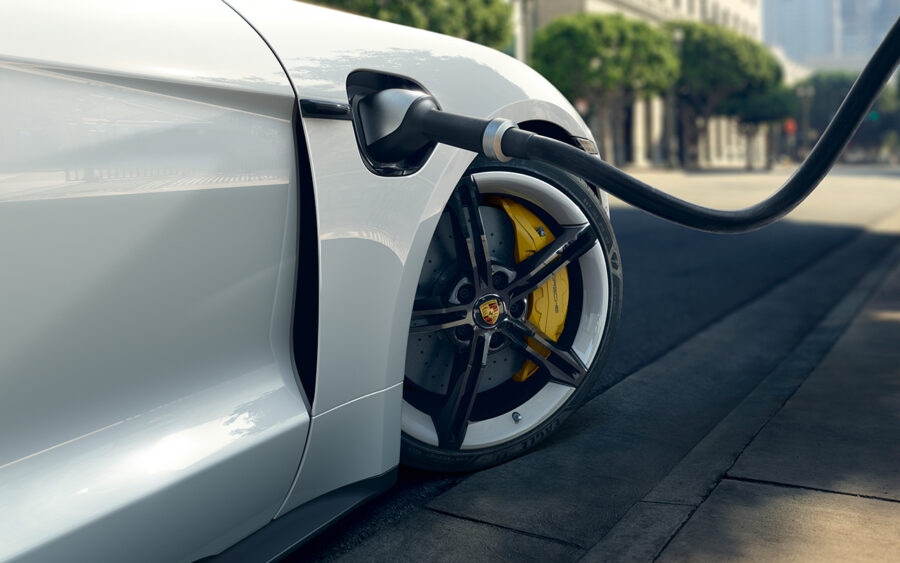
To get close to the average speed possible when conducting the same drive in a traditional car running an internal combustion engine, Porsche deduced that significantly faster charging was necessary. And so, it set about bringing to market the first 800V system. Unfortunately, being a pioneer in this field meant huge expense – there were no ‘off the shelf’ parts available to make Porsche’s desired electrical system. This is widely believed to be the reason no other carmaker beat the Stuttgart brand to the finish line. Porsche had little choice but to develop its own electric motors, on-board chargers and inverters.
Talking of which, Porsche’s electric motors are very special. They follow the tried and tested permanently excited synchronous motor design to begin with, using high-quality permanent magnets to generate a natural magnetic field, but the innovation in the Taycan’s motors comes from the copper wire windings. Porsche replaced the traditional round wires with square wires, bent and then laser welded. The resultant shape lends itself to the ‘hairpin winding’ name and allows Porsche to pack in a lot more copper.
In fact, Porsche claims that, against a conventional winding copper filling factor of forty-five percent, its system manages a whopping seventy percent. This increases power output and torque for the same volume, with claims the shape also lends itself to far greater cooling efficiency. As a consequence of these developments, when launched, Porsche’s electric powertrain had the highest power density (kW per litre of packaging space) on the market. Thankfully, given the likely fiendish expense of that solution, Porsche was able to use existing battery cell chemistry and technology, rather than having to reinvent this aspect of its new energy system.

Porsche EV batteries
For the Taycan Turbo and Taycan Turbo S, two layers of cells comprise what Porsche calls Performance Battery Plus, which benefits from 396 individual battery ‘pouch’ cells, enclosed by a flexible composite foil. These are mounted in thirty-three cell modules, each with a control unit for monitoring temperature and voltage. All of this fits into a battery housing in the floor of the Taycan, located between the wheels in a load-bearing structure. The total energy capacity is 93.4kWh.
Porsche wasn’t only thinking of charging times when it decided upon the 800V system. It wanted Taycan owners to have the option to use the car’s considerable performance over and over again. To help achieve that goal, the manufacturer’s crack team of specialists came up with a holistic heat control concept, integrating the battery with the car’s cooling circuit and a coolant pump. In fact, the heat taken away from the high-voltage components can be stored in the battery, rather than dissipated to the environment. This adds to overall efficiency: in this way, battery temperature can be tightly controlled, not just for safety, but also for performance.
We’re led to believe the target temperature of the battery varies depending on the charge in the battery and on the selected driving mode. This is important, not only to enable launch control, but also to deliver the Taycan’s headline power figures consistently. When the Taycan is plugged in and being charged, battery temperature is automatically brought to a predetermined level. This is independent of the cabin temperature and conditioning, which is set by the car’s occupants.
When on the move, the Porsche Intelligent Range Manager (PIRM) predicts the energy consumption of the car’s various systems – such as air conditioning – and provides an estimated range based on the current driving mode. It can, if it determines the battery charge will be excessively low by the end of the journey (as set in the navigation system), alter the driving mode and even the air conditioning. Interestingly, the Taycan offers further efficiency gains due to using an 800V system.
Look at our earlier equations and consider a situation where a Taycan is driving along at moderate speed, with a low power demand. Thanks to the high voltage, current flow is dramatically reduced, which means lower resistance through all the components, resulting in lower losses. Remember: the energy to heat up the electrical components effectively comes from the battery. Keeping it to a minimum preserves battery charge. This alone has allowed Porsche to optimise the thickness of the cabling, saving some forty kilograms and freeing up room for packaging, too.
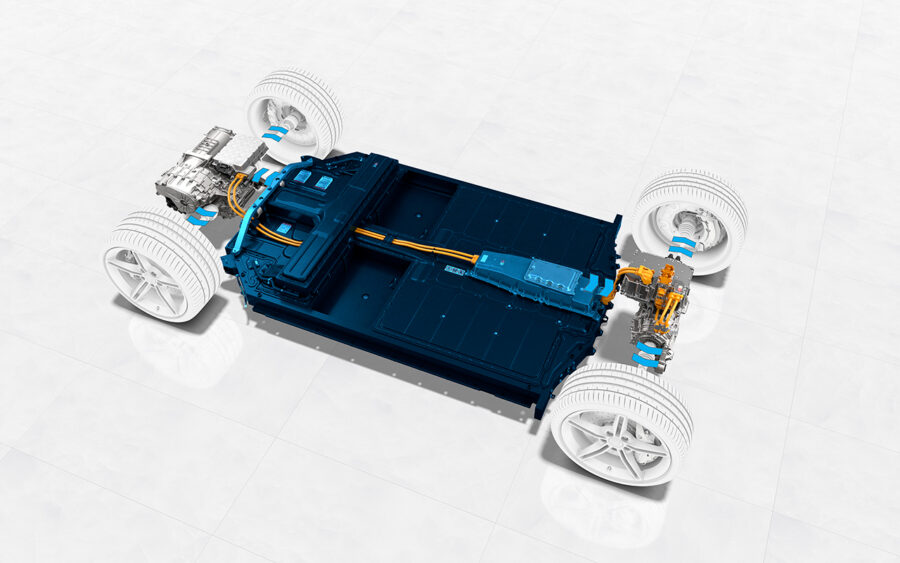
Now, there’s no point Porsche investing a fortune in a cutting-edge 800V electrical system if there isn’t a charging network available to supply it. Back in 2016, Porsche postulated that, while investment and operation of faster chargers amounted to significant costs for operators of electric car charging centres, the cost per kilowatt of supplied charging power reduced considerably when working with higher voltage.
Keep in mind, it takes less time to transfer a given amount of energy to a battery pack for cars which can handle this voltage. The overall energy consumed is no higher, and many of the base charging components that are already used in 400V systems can be reused for 800V chargers. And, of course, as these cars are charging far quicker, more of them can be charged in any given amount of time.
In 2018, Porsche put its money where its mouth is by opening its own fast-charging park boasting 800V technology. This was a pilot project to prove the concept, rather than a sign Porsche is getting into the business of supplying its own general-use public charging stations. It’s fair to assume Porsche’s engineers were aware of the rollout of the much-lauded Ionity high-power charging network when it decided on the Taycan’s technology – at the time of writing, there are more than four hundred Ionity chargers in Europe, with many more to come. Porsche, via the Volkswagen Group, is one of the founding partners of this venture, and is currently the only invested party with a car that can use the full 350kW charging rate.
And what does our beloved Porsche call all this? Porsche Turbo Charging. Of course it does.
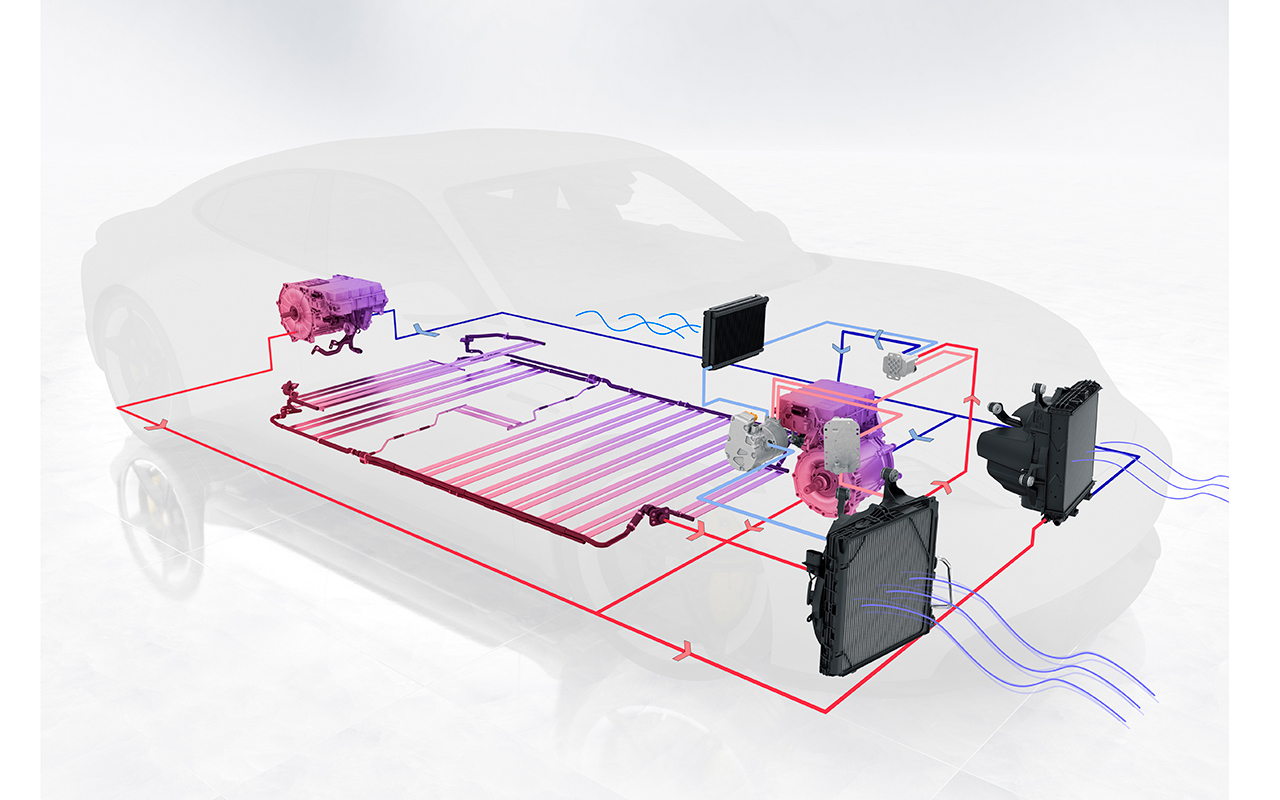
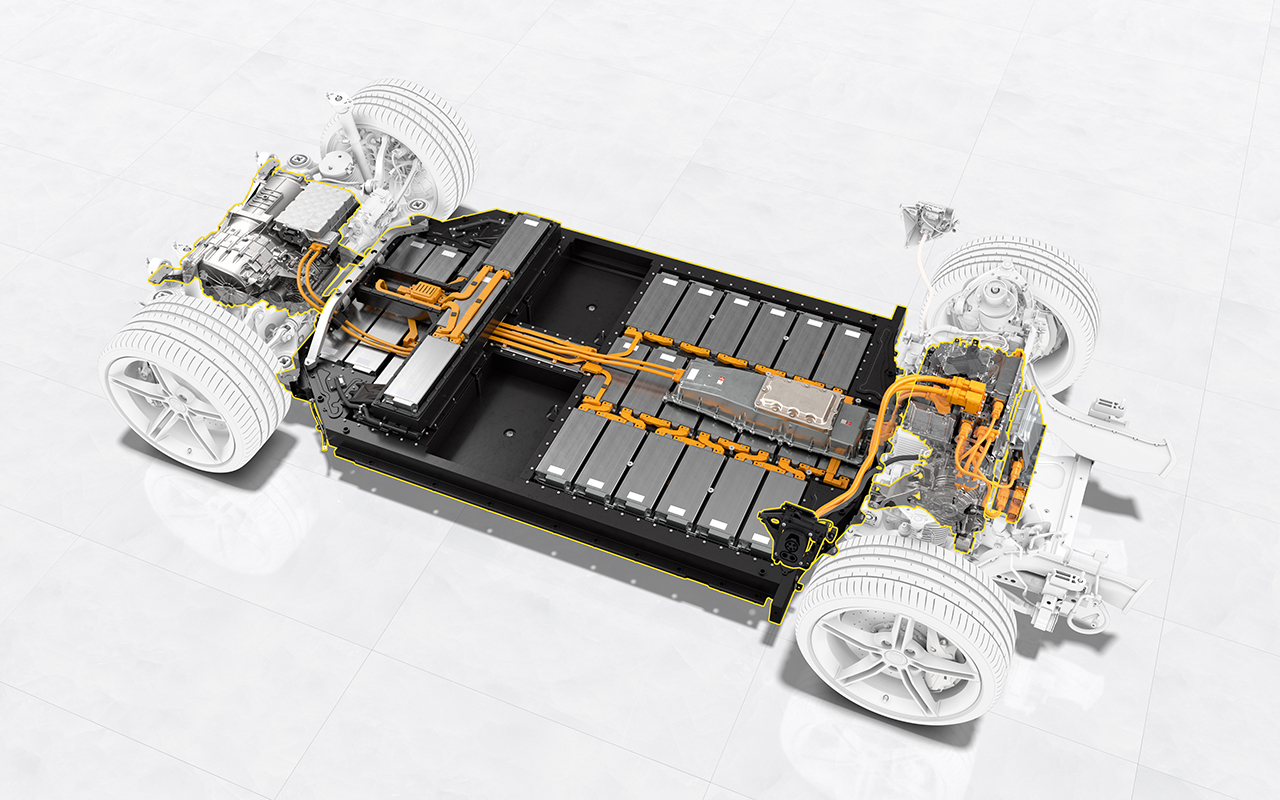

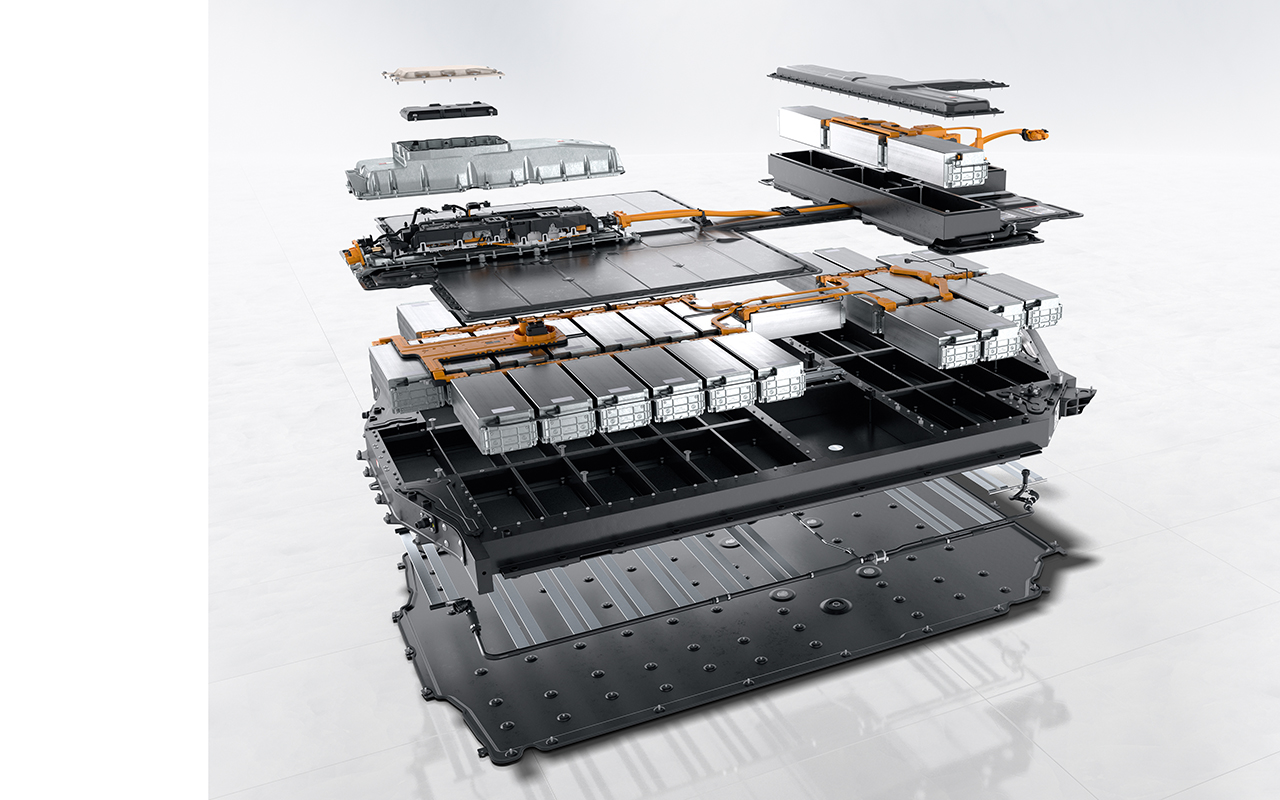
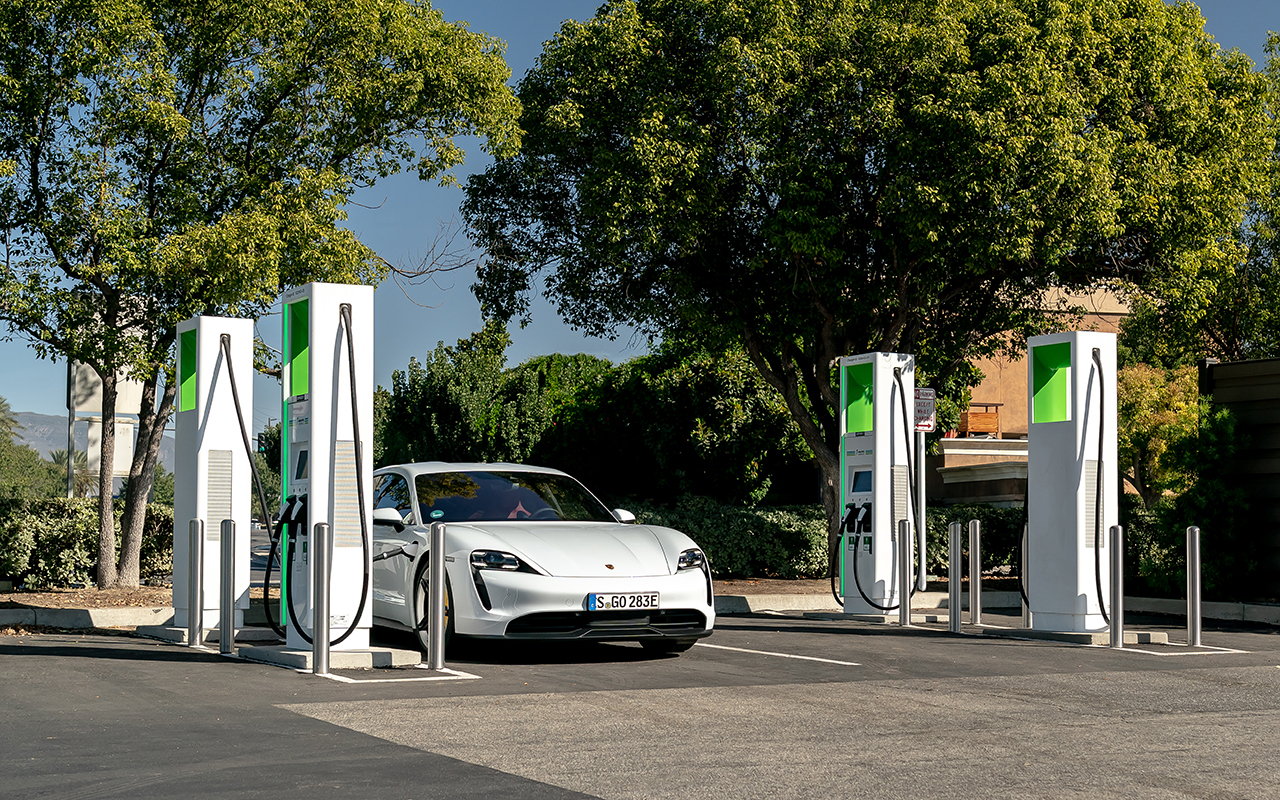
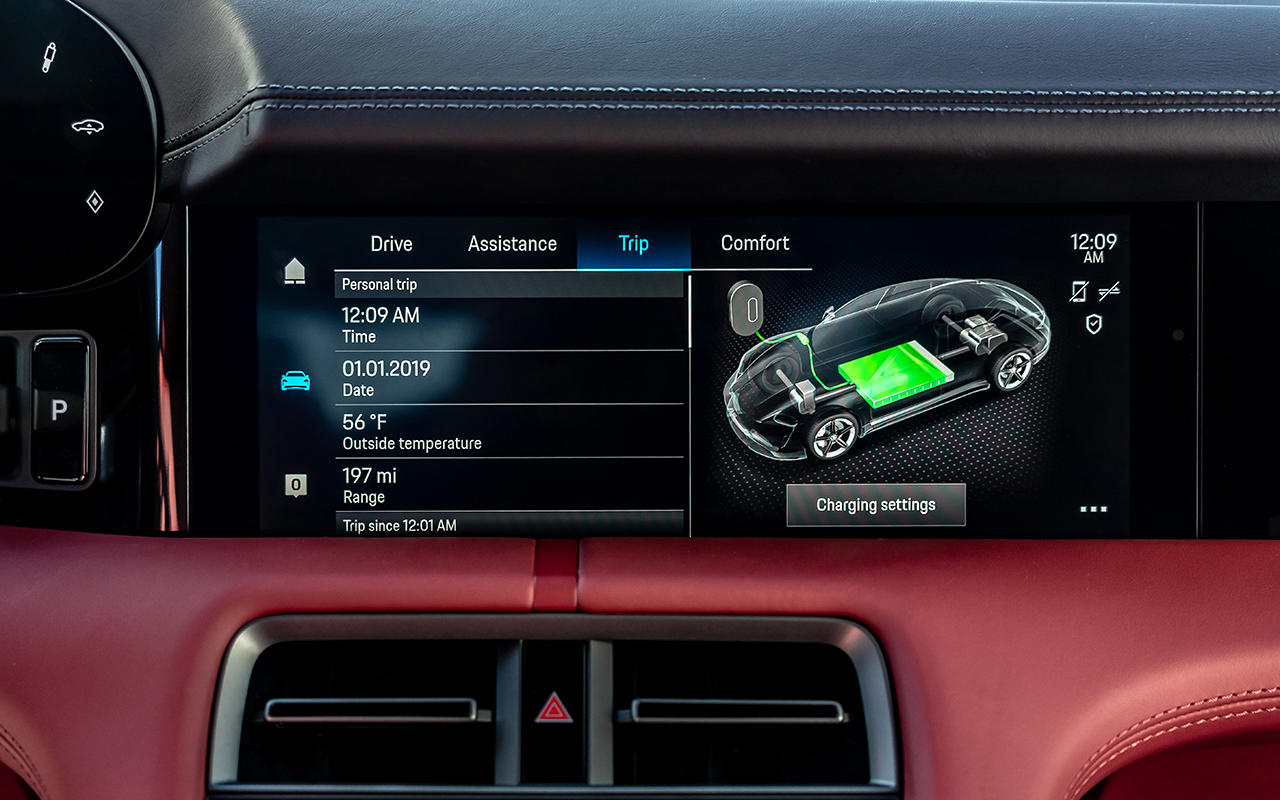

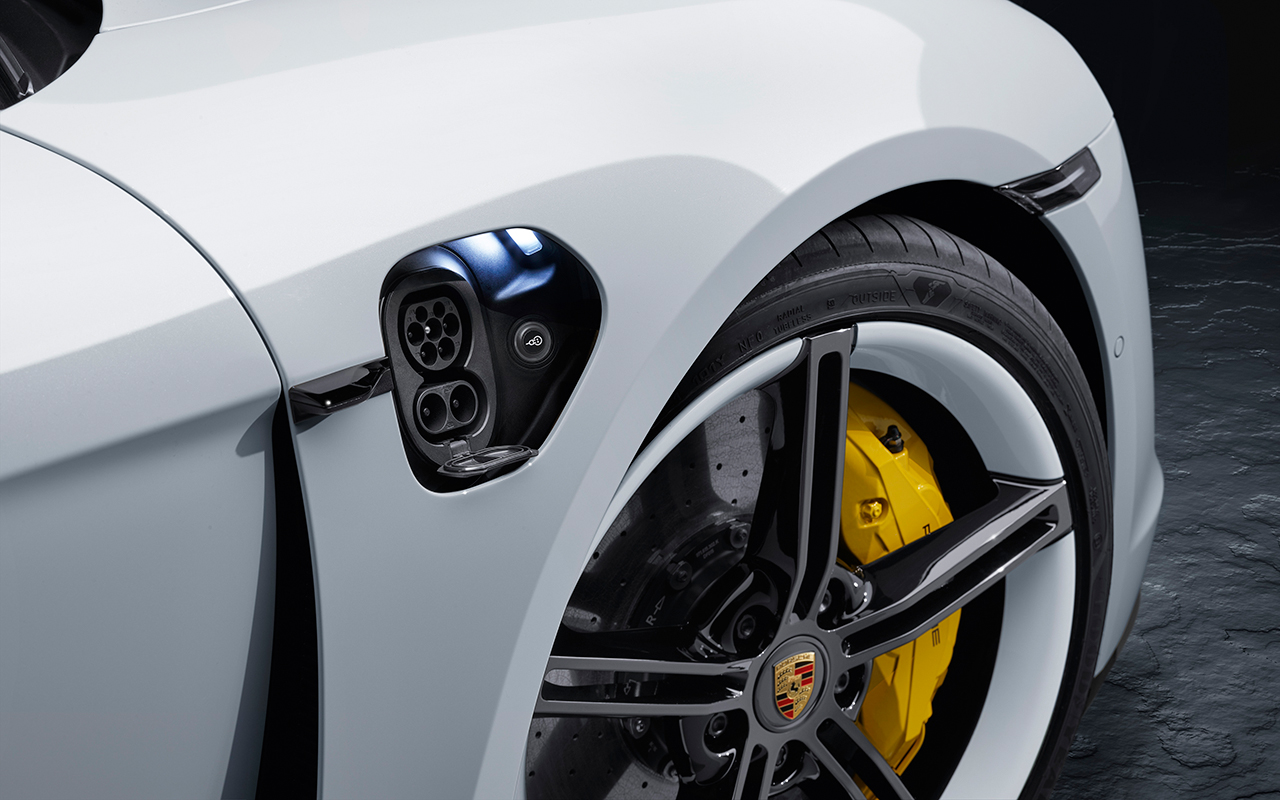
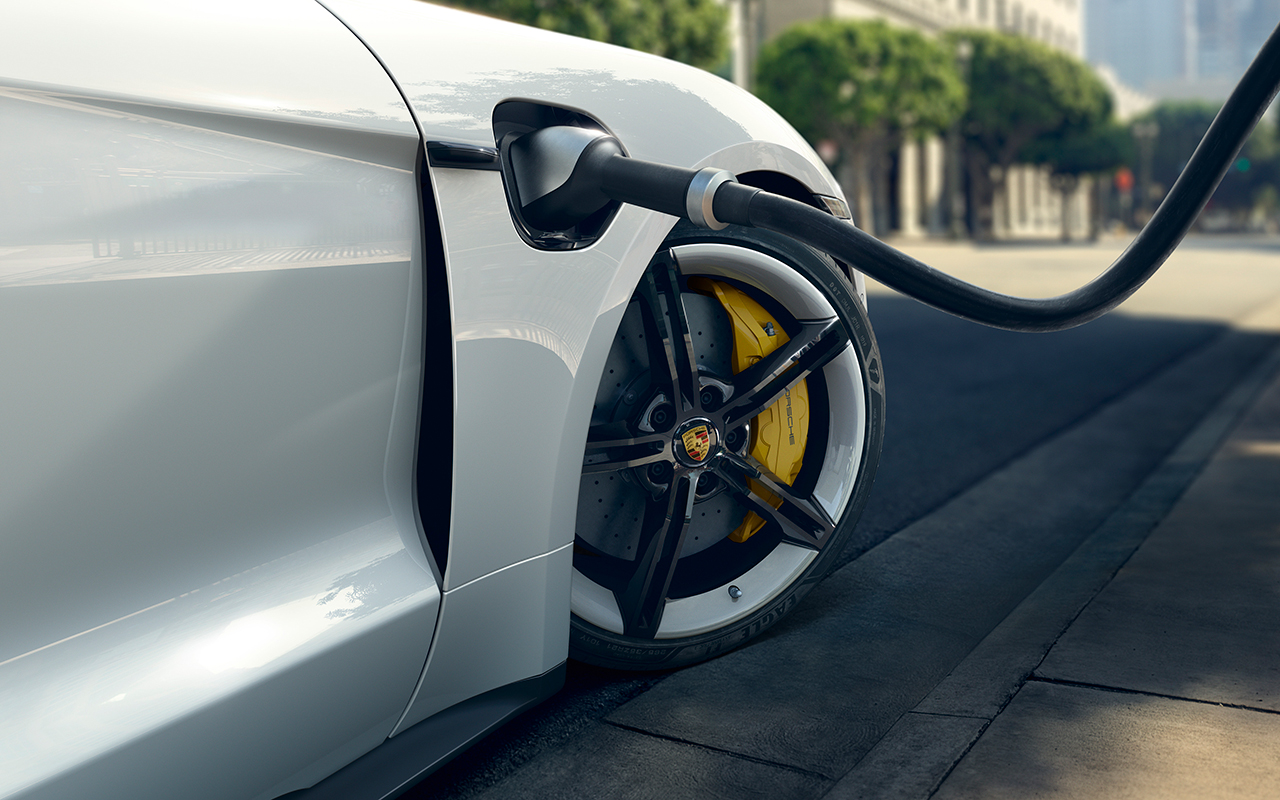