The 996 brought many changes to the 911, chief among which was the water-cooled M96 engine. Here’s the story behind its design and development
Words: Shane O’Donoghue
While Porsche had used water-cooling in many road and race cars prior to the arrival of the 996, the 911 abandoning the air-cooled flat-six was nothing short of momentous. There was a moment when it looked as though the 993 could have had the honour of being the first water-cooled 911 in the brand’s history – Porsche seriously considered using an Audi-supplied V8.
The fact this engine would have required a complete rethink of the 911’s layout was the air-cooled flat-six’s saving grace. Nonetheless, air-cooling was living on borrowed time: compromises, such as increasingly difficult-to-quell noise, cost of manufacturing and limitations on performance were at the forefront of Porsche’s thinking. Thankfully, the future of the manufacturer’s flat-six arrangement (albeit with water cooling) was assured when Porsche took the decision to develop the 996 and the 986 Boxster in parallel, allowing economies of scale.
This approach extended beyond the engine, but as far as the powerplant was concerned, the target was a flat-six with more performance, better fuel economy and lower production costs. The desired engine, codenamed M96, needed to make use of fewer unique parts and be easier to assemble in less time than what came before. Porsche also wanted to reduce the number of joints and seals used, all in the name of reliability and longevity. No pressure on the engineers, then.
M96 engine internals, camshaft and timing
The M96’s crank wasn’t radically different to that of its predecessor. More specifically, the part used for 996 engine production was forged in steel and designed for optimal lightness and stiffness. Indeed, 118mm bore spacing was retained. The part features twelve counterweights and runs in seven main bearings, too.
The seats for these bearings were cast into a new aluminium ‘bearing bridge’ (as Porsche referred to it), essentially a skeletal box frame holding the crankshaft and to which the cylinder blocks and heads are fastened using long tension bolts for rigidity. Within the bearing supports are ducts for bringing oil to the big-end bearings and to the oil jets, which are aimed at the underside of the pistons to keep them cool. Bolted to the crankshaft were six connecting rods of a then new design. Not only are they a good deal longer than those in the 993, they also represented a world-first for Porsche.
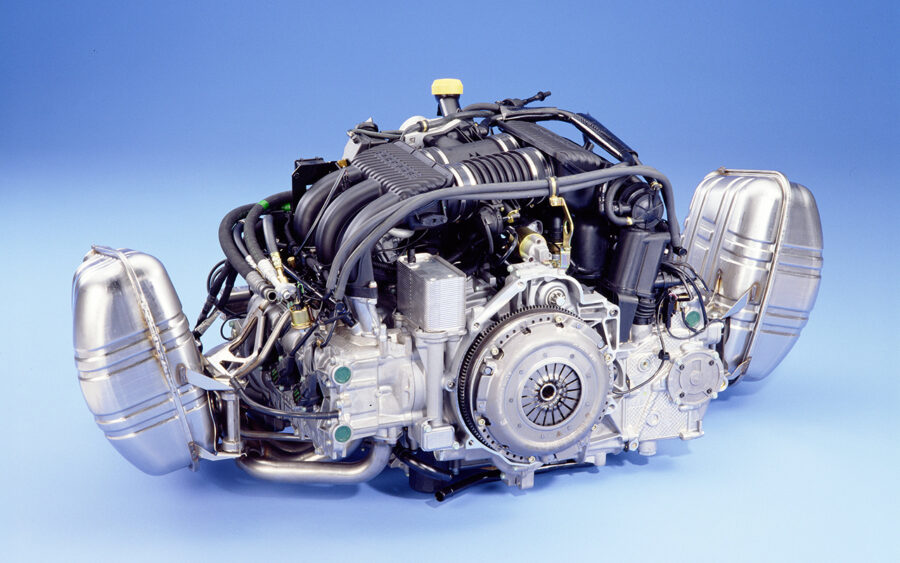
By the time of the 996’s launch, it was commonplace to cast a connecting rod in one piece, then mark it with a laser and force a break along the marked line, creating separate pieces for the rod and bearing cap. This technique has been proven to create a much stronger joint between the parts — due to the crystalline structure of the material — than if the two parts were manufactured separately and machined to suit. Porsche’s innovation came from the use of forged metal instead of sintered, which means the connecting rod can cope with much higher stresses.
Likewise, while the 986 Boxster’s engine made do with cast pistons, the 996’s M96 received more expensive forged items. Featuring a recess in their crowns to accommodate valve lift, they’re much simpler in design than those used in the 993. This is because the twin-spark combustion chamber, complete with its patented airflow method, was abandoned for the 996. Instead, a single centrally mounted spark plug was employed for the M96 and, at long last for the 911, a four-valves-per-cylinder inlets, as had become the norm in high-performance engines across the world.
Before we look into the cylinder heads and what’s opening and closing the valves, it’s worth mentioning the cylinder blocks. In comparison to the same-age Boxster’s engine, the 996’s M96 flat-six used a 10.5mm wider bore (96mm) and a 6mm longer stroke (78mm), resulting in swept capacity of 3,387cc. The liners were cast with the block, which wasn’t unusual, but Porsche also wanted a high-pressure die-casting technique to allow for high-volume production.
This was not possible using existing cylinder bore treatment methods, which is why Porsche adopted a new system from Kolbenschimdt Pierburg AG. Known as Lokasil, it considerably sped up the process. At this stage of our story, those in charge of early 996s may well be cursing this key decision; Lokasil liners aren’t exactly known for their durability.
Another well-known weak point is the bearing of the intermediate shaft (IMS). This shaft sits below the crankshaft and is driven from the crank via a short chain. In turn, via chains, the intermediate shaft drives the exhaust camshafts on either side of the engine. Ingeniously, Porsche was able to shorten the flat-six by inserting the long chain drives in the space created by the offset cylinders. Lest we forget, the cylinders are actually offset in a boxer engine by the distance between the crankpins. That’s unavoidable, but Porsche cleverly made use of that space. The use of an intermediate shaft furthermore made that possible, while also slowing down the speed the long timing chains travel at, thereby reducing noise and chain wear.
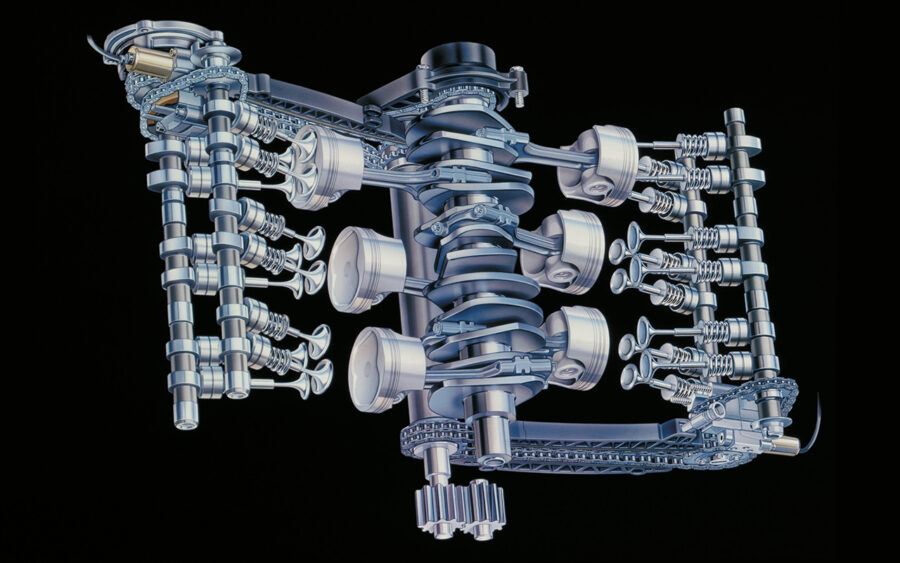
Another short timing chain on each side of the engine drove the inlet camshaft from the exhaust. Between the two camshafts — again on each bank of the unit — sat the VarioCam system altering inlet valve timing by adjusting chain tension according to the demands of the engine control unit. On start-up, idle and low revs, there’s no valve overlap, allowing for stable idle, even if the VarioCam unit fails. At 1,500rpm, the overlap is increased to boost torque in the mid-range and, at 5,820rpm, it switches back to its original state, presumably to make use of the late valve closing in preference to overlap.
In the pursuit of more performance, and to distance the 911 from its new Boxster sibling, the 996’s engine received bigger valves and ports with higher lift for the inlet valves. The cast iron camshafts are carried in four bearings and the cam lobes operate on maintenance-free hydraulic cup tappets. The valves are closed by springs with a conical shape, which allowed for smaller and lighter valve retainers. Further cleverness was found in the design of the cylinder head casting, which was the same on each side of the engine, with unique machining, obviously. It was the same story for the camshaft covers and tappet carriers within.
M96 induction and exhaust
Sitting atop the engine is a plastic inlet manifold, with three runners clearly visible to each side of the engine, along with two plenum chambers. These were joined by two tubes, one of which features a butterfly valve opened and closed by the engine management system to alter the resonance in the intake system when required to improve volumetric efficiency. This is the measure of how much air (in terms of mass) you can get into an engine’s cylinder, compared with the theoretical amount. More air in the cylinder means it’s possible to burn more fuel, which translates into more energy released in a given combustion cycle, resulting in more torque at the crankshaft. Simply put, higher volumetric efficiency equals more torque and, because power output is directly proportional to torque, more power.
Due to the air being sucked into cylinders on alternating sides of the engine, a forward and back pressure wave occurs within the pipe connecting the two plenums. The position of this pressure wave at any given moment depends on the geometry of the inlet manifold and engine speed. At a certain speed, the pulsing of air reaches what’s referred to as its ‘natural frequency’ and resonance occurs — the pulse from one plenum to the other will be in phase with the intake strokes. In turn, this results in higher air pressure in the inlet ports when the inlet valves are open, leading to a greater mass of air in the cylinder and therefore an increase in volumetric efficiency and torque.
The engine speed at which resonance occurs can be tuned by the geometry of the inlet manifold, but it’s always a compromise because there’s a very narrow rev band over which resonance is useful unless you introduce a variable resonance manifold, as first used on the 964 and also employed here. The butterfly valve in the M96 is open up to 2,700rpm, then closed from this point up to 5,100rpm, before being opened again all the way to the redline. The result is a significant increase in the engine’s volumetric efficiency.
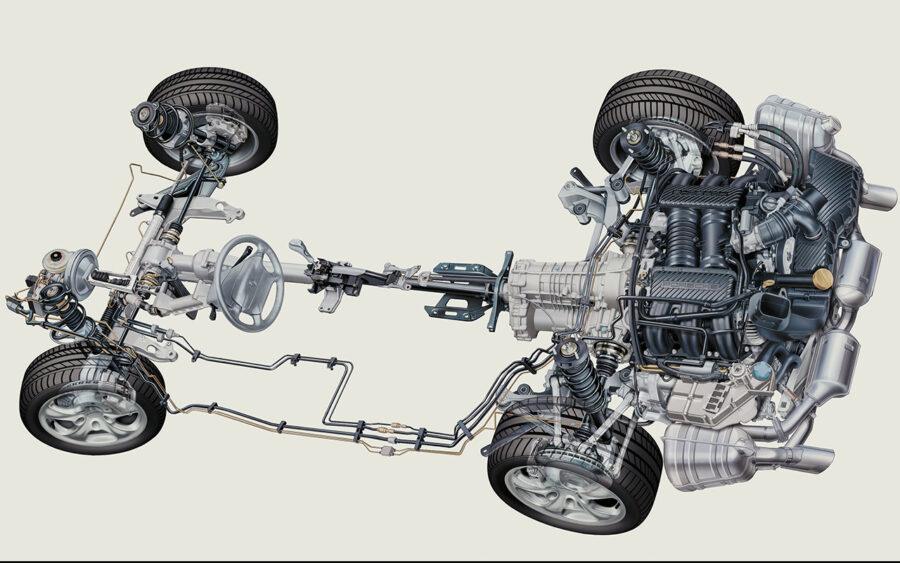
Also part of the new inlet design was a Helmholtz resonator, which was used to tune the sound of the intake and gives the 996 its characteristic bark. Helmholtz resonance (named after Hermann Ludwig Ferdinand von Helmholtz, a German physicist who experimented with the science of sound in the 1850s) is the noise air makes from resonating in a cavity. Think of blowing across the top of a bottle or the uncomfortable ‘helicopter’ noise that some moving cars exhibit when you crank open one of the windows or the sunroof. This phenomenon encouraged the introduction of specially designed air boxes, often separate from the air filter box, the sole purpose of which is to tune the sound of the intake.
The exhaust system, despite strict emissions legislation, was simpler in design than the pipework found on air-cooled engines, chiefly because classic 911s relied on toasty exhaust temperatures for cabin heating. For the 996, a more efficient and, crucially, lighter heating system was deployed. Further evidence of Porsche’s commitment to reducing production costs was found in the design of the 996’s large exhaust mufflers — a single set of tools could manufacture mufflers for either side of the engine, as opposed to each part requiring its own tooling.
Cost cutting, however, is blamed for the lack of proper dry-sump oil lubrication. Porsche references the design as ‘integral dry-sump lubrication,’ but it’s not quite the same thing and has been found to be insufficiently capable of maintaining the correct oil pressure when dealing with sustained high-g cornering, despite the use of individual scavenge pumps driven by the exhaust camshafts.
M96 cooling system
The M96 water-cooling system is fairly conventional. It uses a ‘crossflow cooling’ concept, where the coolant flows from the exhaust side to the inlet side of each cylinder bank. The flow splits to cool the tops of the cylinder liners and the combustion chambers. 996s with manual transmission featured two air-to-water radiators mounted in the front of the car, while those with the Tiptronic S automatic gearbox gained a third radiator. Moving away from air cooling for the 911’s flat-six may have been seen as a dramatic change, but its implementation was entirely conventional and already well-established elsewhere in the Porsche product range.
When the 996 debuted for the 1997 model year, the 911 Carrera’s engine produced 296bhp at 6,800rpm and 258lb ft torque at 4,600rpm, revving to 7,300rpm. This compares with the outgoing 993’s 281bhp at 6,500rpm and 250lb ft at 5,250rpm.
You may think these are small gains for a huge amount of engineering work, but where the 911’s air-cooled engine was at the end of its development path, the evolution of the water-cooled flat-six was only just beginning: Porsche would go on to make the engine quieter, more economical, lighter and much cheaper and quicker to produce.

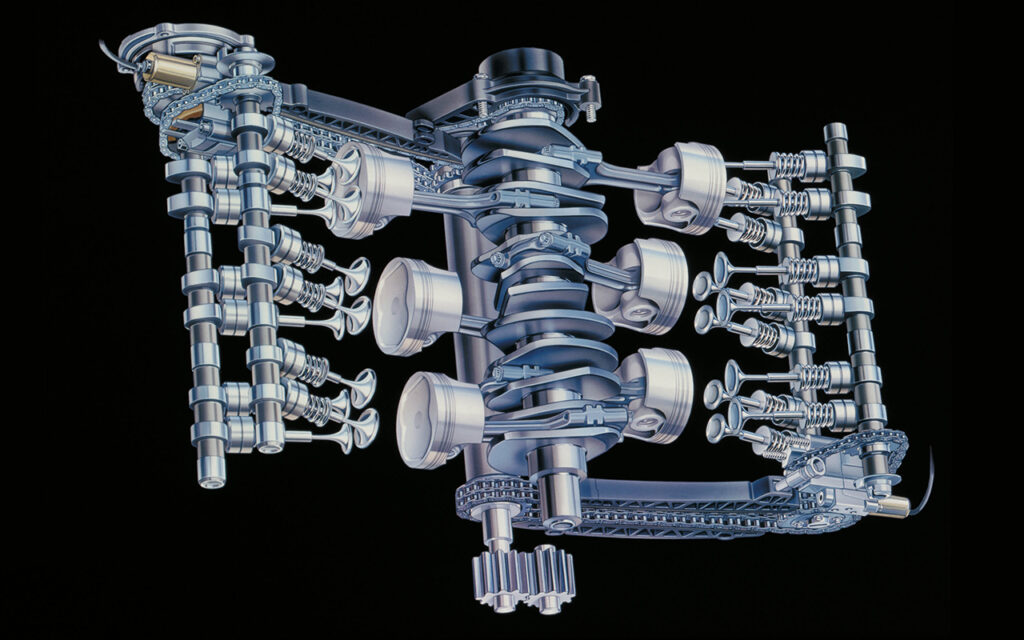
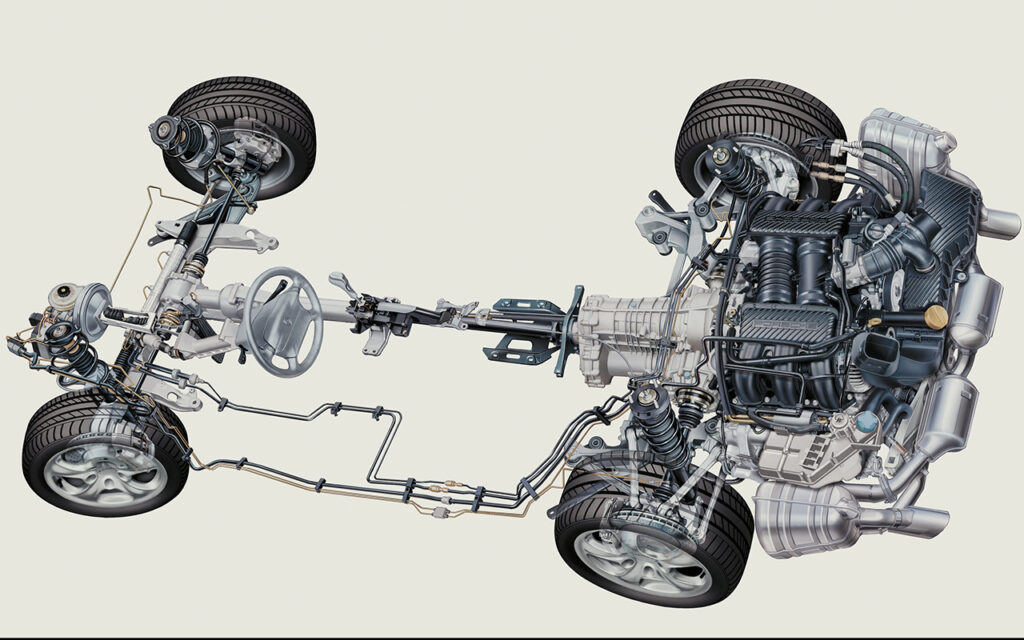
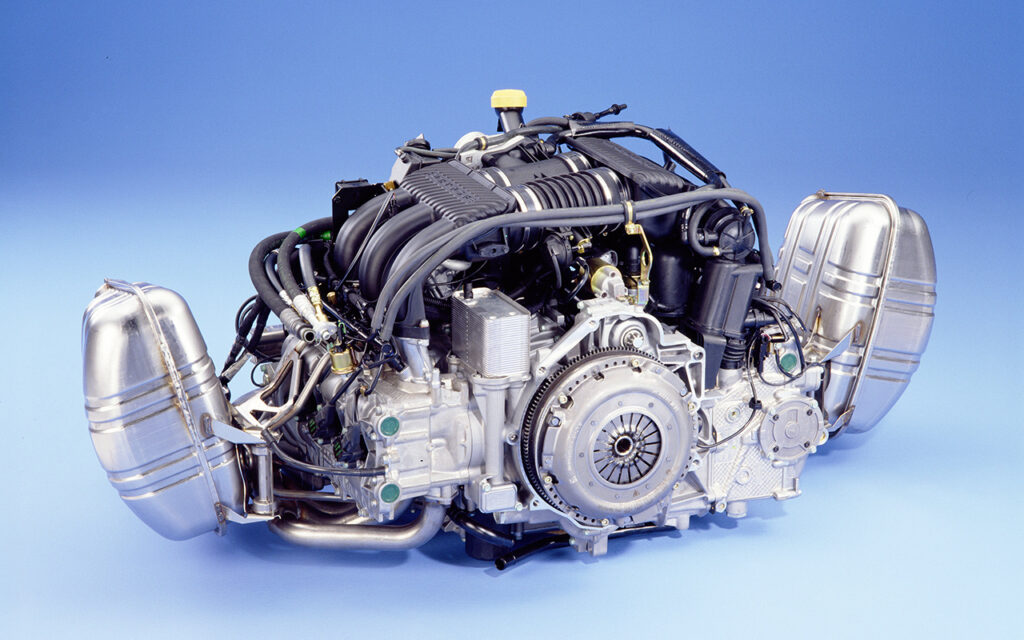
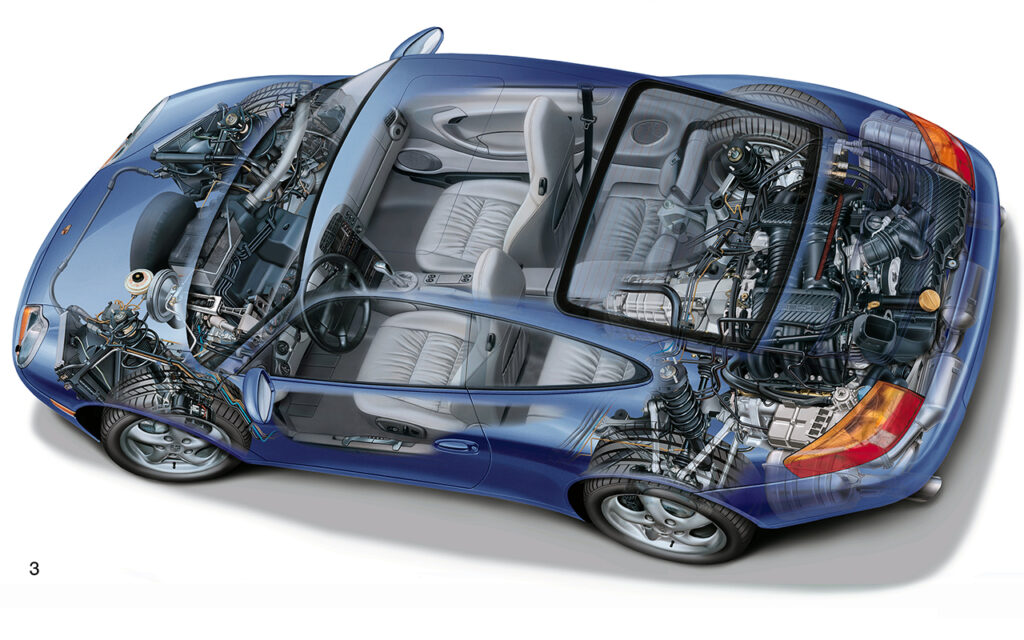
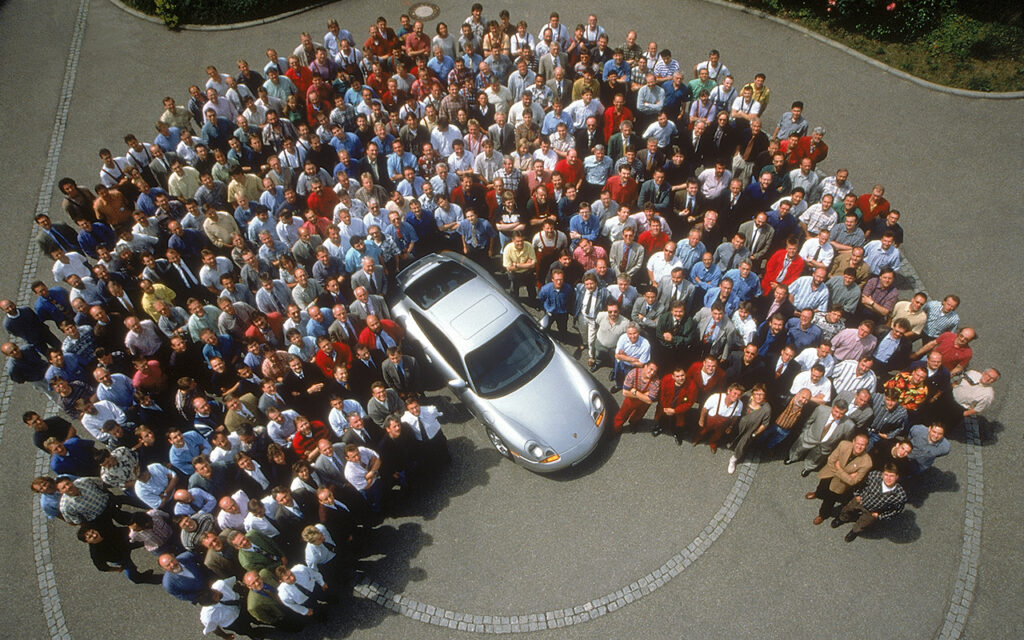
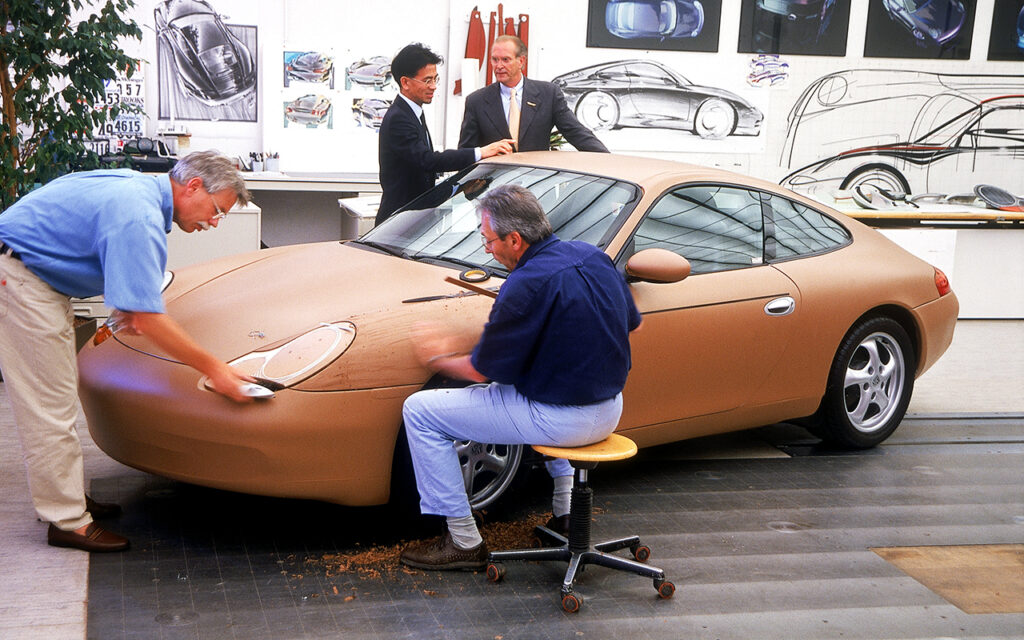